Introduction
Cementir, a global cement player with Italian roots, is the kingpin in white cement (with a 20% market share excluding “off”-white cement). The company has substantial exposure to the European markets but diversifies with its presence in the Mediterranean, North America and Asia. The company strives to develop strong local market share in grey cement and a noteworthy global market share in white cement.
Like its French peer Vicat, Cementir is a family-driven business that has maintained a solid balance sheet throughout its volatile industrial cycle, with its net debt/EBITDA consistently below 3x. It stands unique as it dodged costly acquisitions during the top of the cycle (2007-08) and, ergo, avoided the need for fresh-but-dilutive capital at the bottom of the cycle (2008-09).
Cementir believes in fair-priced acquisitions which have strategical location and well maintained assets. Its past deals helped it to develop a white cement franchise with strong and recurrent cash flows (mainly linked to the renovation market) which could be the cash cow to a careful expansion in the bigger but more cyclical grey cement market. Yet, with the current focus on sustainability and digitalisation, we evaluate the likelihood of its inorganic growth as low.
Operations
Cementir has operations in 18 countries across five continents. In addition to white cement, it is involved in grey cement, ready mix, aggregates and the processing of urban and industrial waste.
What makes Cementir unusual is its exposure to the consolidated and more lucrative white cement business (20% global market share, excluding “off-white” and lower quality Asian products). White cement provides a great white space opportunity as it trades at twice the price of grey cement (local comparison) and accounts for about 1% of grey cement volumes. Given its higher unit value in comparison to white cement, it can be more easily transported, opening the company’s gates to global markets. This has in turn made Cementir the leader of traded flow, with export sales representing about 25% of total exported volumes globally. Furthermore, its local presence with a sales force and/or controlled logistic networks in about 20 key target markets enhances its exports. The group aims to export 50% of the white cement produced by 2020, which is an ambitious but achievable target in our opinion.
White cement relies on scarce yet extra-pure limestone, accompanied with sand, gypsum and alu silicates. These hardly exist in certain countries such as Brazil, Australia and parts of Africa. The chemical composition of the limestone used in white cement is such that the burning process requires a higher temperature and eats up roughly 50% more energy as compared to grey cement.
Waste management as part of the cement value chain
For a decade, Cementir has been strategically including waste management in its value chain. In 2009, Cementir entered the Turkish waste management business through the acquisition of Sureko AS and reinforced its presence through the acquisition of Recydia in 2011 (waste management and renewables business). It was then complemented by the acquisition of NWM Holdings (UK) which collects, treats, recycles and disposes of waste. Since Cementir has no cement plants in the UK, we believe that the goal is to use this waste as fuel in the Denmark kilns to reduce energy consumption (as waste has higher calorific value than traditional fuels) and leave a greener footprint because the wastes would have been incinerated otherwise as well. Cementir’s waste business’s standalone profitability might seem low but it enables the group to address environmental issues significantly.
Contrarian strategy?
Cementir has grown from a medium-sized Italian “single-country” and “single-product” operator into a fully-fledged multinational company, without any increase in share capital, thanks to surplus operating cash flow generation.
In 2001, the Cementir Group embarked on its geographic diversification process, by acquiring Cimentas in Turkey. This was followed by a product diversification through the acquisition of Aalborg Portland in 2004, a white cement manufacturer.
However, the most radical transformation of the Cementir Group portfolio came between 2016 and 2018. It acquired the cement and concrete business of Sacci SpA (2016), expanded its international presence by acquiring CCB (2016), sold off all Italian assets in 2018 (with only the central headquarter and some trading businesses remaining in Italy) and, lastly, acquired a majority shareholding in Lehigh White Cement Company (LWCC) in the US (2018) – making Cementir a leader in this promising niche market with a market share of ~20%.
The company is now present in several regions across five continents. The idea is to be exposed to both emerging markets, which offer strong but volatile growth, and developed markets, which have slower but more consistent growth. The company’s operations span six key regions: the Nordic & Baltic, Belgium, North America, Türkiye, Egypt and Asia Pacific. The production facilities are vertically integrated for aggregates, cement and concrete in Denmark, Belgium and Türkiye. Denmark holds a prominent position in both grey and white cement and concrete, while Sweden and Norway lead in the concrete sector. Türkiye’s operations focus on industrial waste management. Meanwhile, the activities in North America, Egypt and Asia Pacific are exclusively dedicated to white cement production.
Industry analysis
Expected growth higher for white cement
There is an ongoing commercial push to “create and grow the market” for white cement while the market for grey cement is demand-led. White cement is a more profitable premium business. While grey cement is a standardised €200bn market with around 2bnt of production per year excluding China, white cement is a €4bn niche market with only about 20mt of production per year.
The growth in the white cement market is expected to be higher than that of grey cement over the medium term because:
- there is a cannibalisation effect of grey cement by white cement due to the added functionalities/applications it offers;
- cement usually represents less than 5% of total construction costs and white cement is only twice the price of grey cement, thus demand is inelastic to prices;
- white cement can replace grey cement in practically every application;
- there are virtually unlimited applications for white cement: pre-stressed concrete façades, paving blocks, artificial stone, Glass-Fibre Reinforced Concrete (GRC) façades, Ultra-High Performance Concrete (UHPC), dry mix mortars and Ready Mix Concrete (RMC);
- a defining feature of white cement is the possibility of producing coloured ready-mix or dry admixtures by mixing it with pigments.
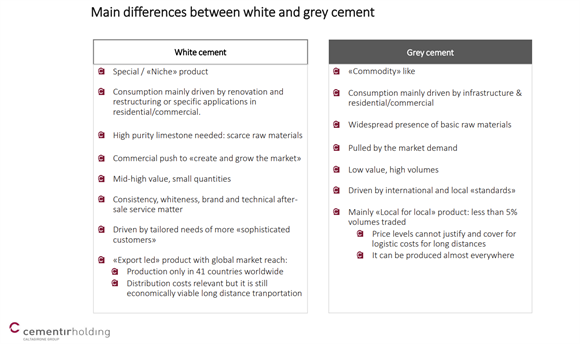
INDUSTRY TRENDS
Global warming
With the increase in global temperatures, the demand for sustainable yet affordable materials is increasing. The manufacturing of cement is responsible for approximately 5% of global CO2 emissions. Thus, this industry is one of several where emission reductions will be key to significantly lowering global emissions. However, the decarbonisation levers are limited. The first lever employed by companies is switching fuel to use waste as an alternative fuel, which allows them to mitigate CO2 emissions during the fuel combustion stage. The second lever is the reduction of clinker, as its production is the most energy-intensive step in the cement manufacturing process, resulting in substantial CO2 emissions. To put things into perspective, of the CO2 emitted by the cement industry, around one-third results from the combustion of fuels, while about two-thirds comes from the calcination process used to produce clinker. Even though alternatives for clinker are being explored, they remain limited; the most commonly used alternatives are fly ash and blast furnace slag. These alternatives can offer different mechanical properties compared to clinker and require adjustments in the construction process and additional certifications, making them more costly. Moreover, regulations play a crucial role, and the cement industry is massive and well-established, making it difficult to change production processes radically. Due to these challenges, carbon capture is an important technology for the cement industry to reduce CO2 emissions significantly.
Alternative fuels
In order to decrease the environmental impact of the industry, improve the competitiveness of cement companies, and provide a viable and convenient end-of-life option for waste and industrial by-products, the use of alternative fuels is evolving.
CO2 taxation
This mechanism allows industrial companies to pollute, provided they hold allowances. There are two types of allowances: free and auctioned. However, these allowances are set to decrease at a faster pace in the coming years to achieve the targets outlined in the “Fit for 55” proposal. Indeed, a new reform established by the EU raises the linear reduction factor from 2.2% to 4.3% from 2024 to 2027, and to 4.4% from 2028 to 2030. Furthermore, the reform includes two one-off ‘rebasings’ of the cap, reducing it by 90 million allowances in 2024 and an additional 27 million in 2026. As the increased climate ambition within the EU may heighten the risk of carbon leakage, the Council and Parliament agreed on a phase-in plan for the Carbon Border Adjustment Mechanism (CBAM) to price imported goods based on their embedded emissions. Starting in 2026, the CBAM will be gradually implemented as the free carbon allowances are progressively phased out to zero by 2034. As the allowances decrease, the carbon price is expected to increase in the coming years. Thus, companies that have not been able to significantly reduce or capture most of their emissions will incur substantial costs to continue their operational activities.
Cementir’s actions
The company’s decarbonization plan aims to accelerate sustainability efforts with a target to reduce CO2 emissions by 36% in grey cement and 19% in white cement by 2030, relative to the 2020 levels. The company has allocated “green capex” to be invested in sustainability initiatives focused on four key areas:
- Alternative Fuels and Renewable Raw Materials: Increasing the use of alternative fuels (>70% for grey cement), reducing clinker ratios through materials like calcined clay and fly ash, and incorporating green power and lower-carbon fuels.
- Low Carbon Cements: Launching eco-friendly products such as FUTURECEM®, Aalborg Extreme™, and Aalborg Excel™ with reduced clinker content and enhanced performance.
- Operating Efficiencies and Circular Economy: Upgrading kilns to reduce heat consumption, increasing alternative fuel use, recovering heat for electricity generation, recycling waste materials and implementing Carbon Capture and Storage (CCS) in Denmark by 2030.
- Digitization of Key Processes: Implementing green transportation (hybrid trucks), optimizing logistics, adopting eProcurement and using predictive maintenance.
These initiatives are designed to support a more sustainable value chain while advancing the company’s decarbonization goals
Urbanisation
The number of people living in cities increases by 50 million every year, and this figure continues to grow. By 2050, an estimated six billion people — or two-thirds of the world’s population — will live in cities. This growth in urbanisation will drive the demand for durable yet affordable workplaces and homes, which will in turn increase the demand for cement.